Ball valves are widely used because of their durability, strength, and affordability. Simple to install, they have a quarter-turn operation that makes piping systems more efficient. The robust nature of Ball valves has led to their widespread use in a range of industries, including chemical processes, petroleum, and water treatment plants.
Although they’re an easy choice for most applications, there are a few drawbacks you should be aware of when selecting the correct valve for your application. At John Valves, we help businesses choose the right valves for their requirements. Here, we explain the advantages and disadvantages of ball valves.
What is a Ball Valve?
A ball valve is cylindrical in shape and has a hollow and pivoting ball as the flow control element. When the ball is open, the hole through the ball faces the flow, allowing fluid to pass through. When the handle of the valve is turned 90 degrees, the ball closes and the flow of fluid through the valve stops. When the valve is open, the handle (or lever) is perpendicular to the direction of flow, making visual indication of the status of the valve easy. The biggest benefit of ball valves is their long service life and reliable sealing capabilities.
1-Piece Ball Valves
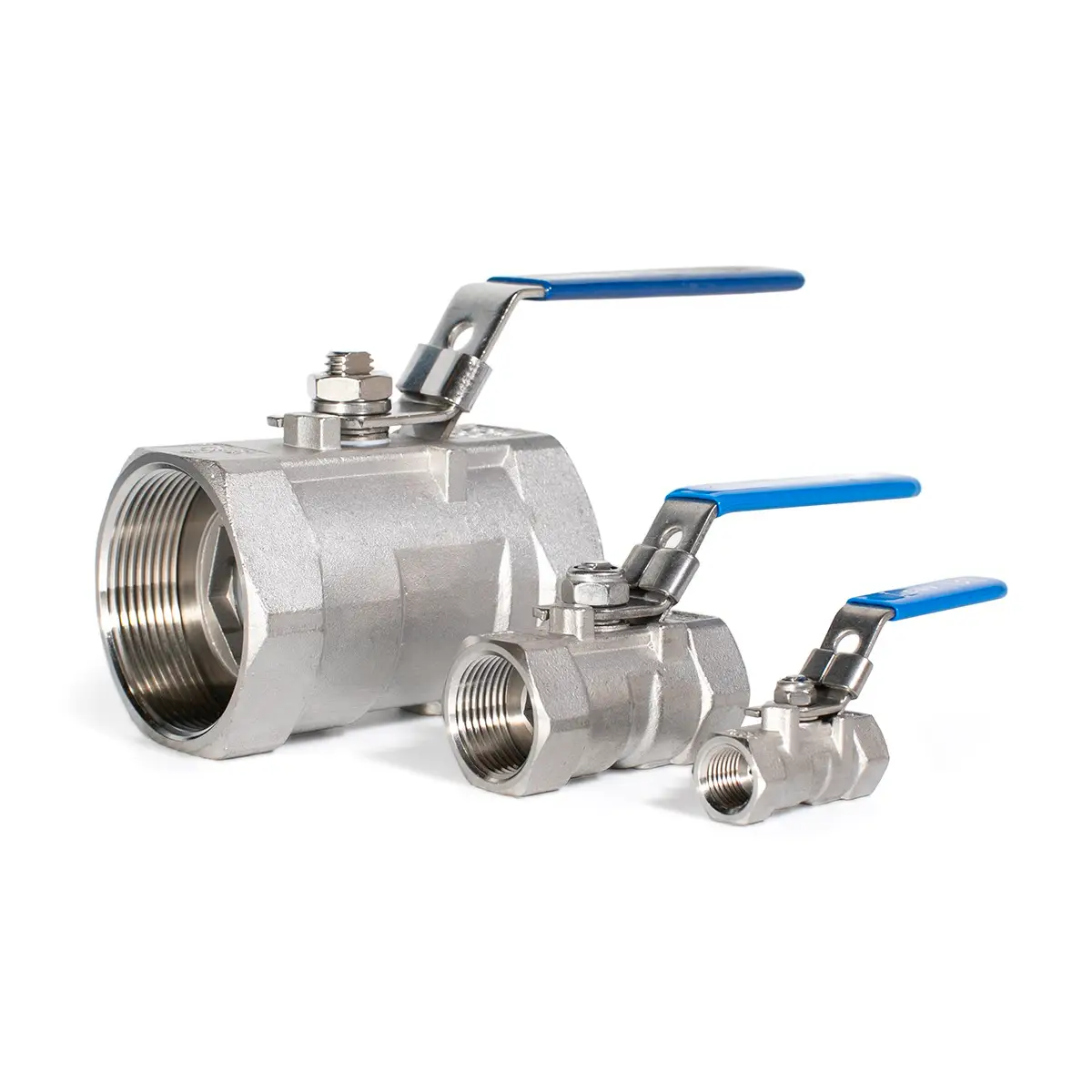
1-piece ball valves are the most economical option and are designed for simple on-off operations. They comprise a single body piece that houses the ball, making them very compact and lightweight. They are best suited where maintenance is not expected to be frequent, and the cost is a significant factor.
2-Piece Ball Valves
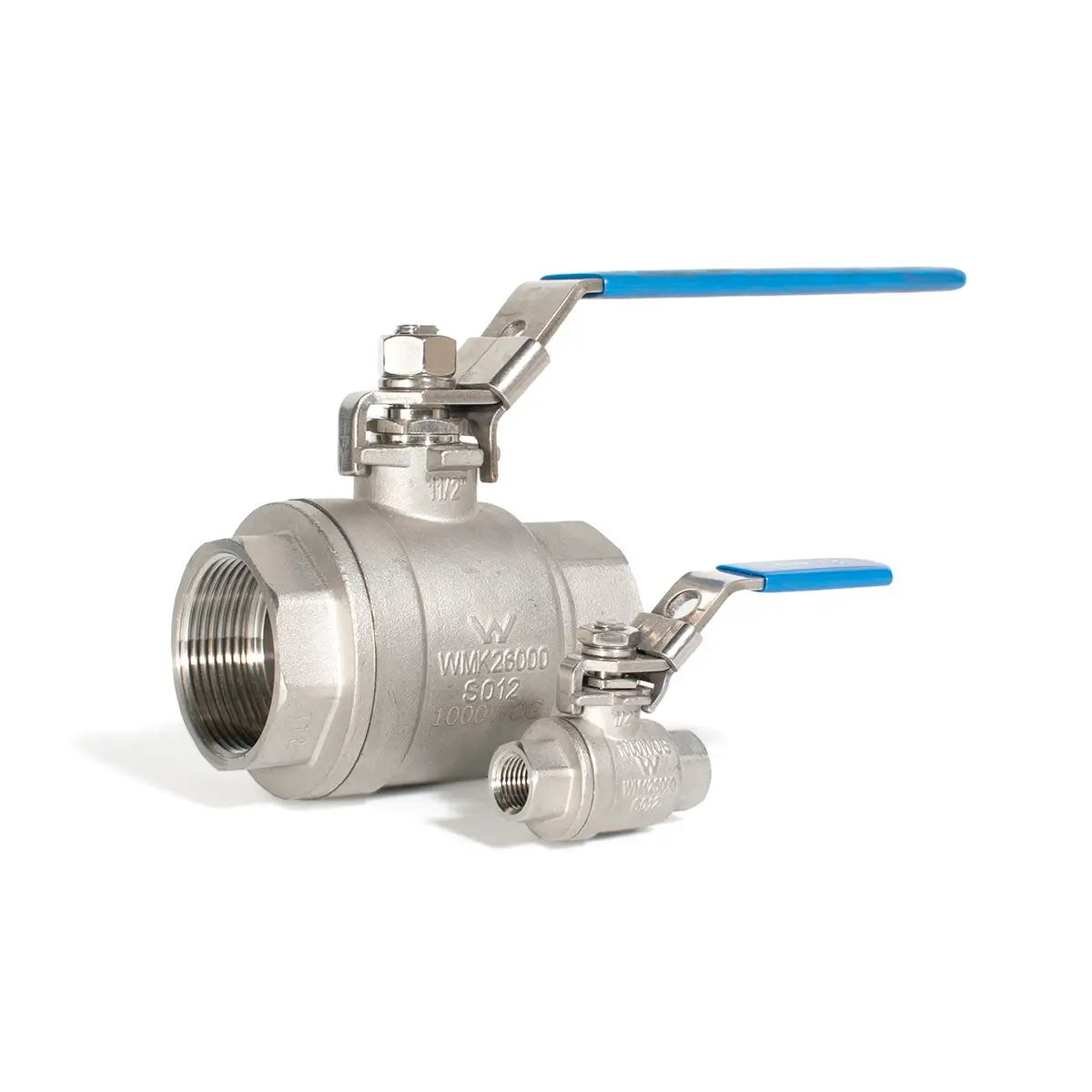
2-piece ball valves are a step up in terms of maintenance and repairability. They consist of two separate pieces, with the connection usually occurring around the middle of the valve. This design allows for easier disassembly and access to the internal components, making them suitable for applications where periodic maintenance or inspection is required.
3-Piece Ball Valves
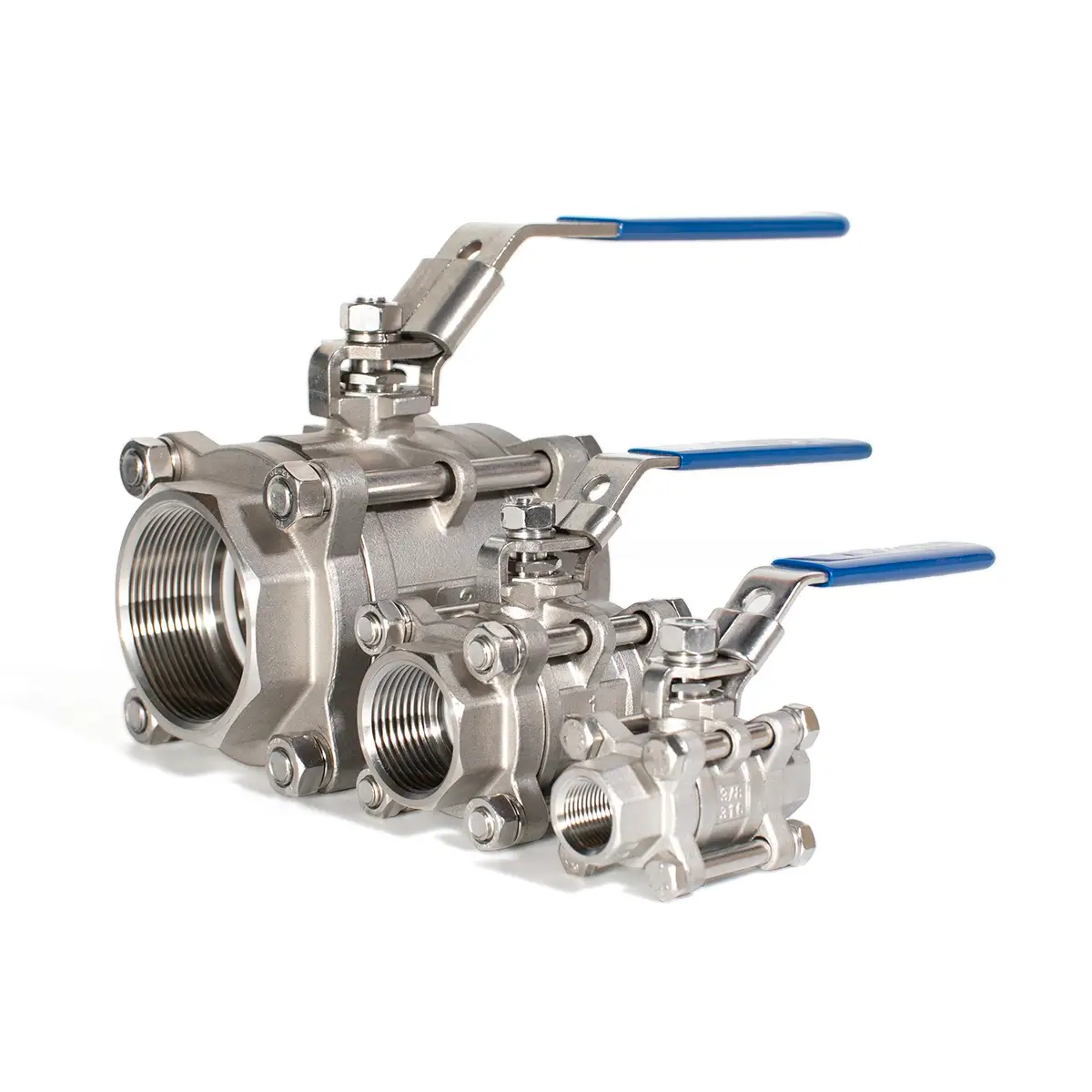
3-piece ball valves are designed for maximum durability and maintainability. They are constructed from three separate pieces, allowing the valve body to be removed without disturbing the pipeline. This feature is particularly beneficial in critical systems where minimal downtime is crucial. 3-piece valves are used in applications requiring regular cleaning, repair, or inspection, and they can handle higher pressures and temperatures than their 1 and 2-piece counterparts.
Flanged Ball Valves
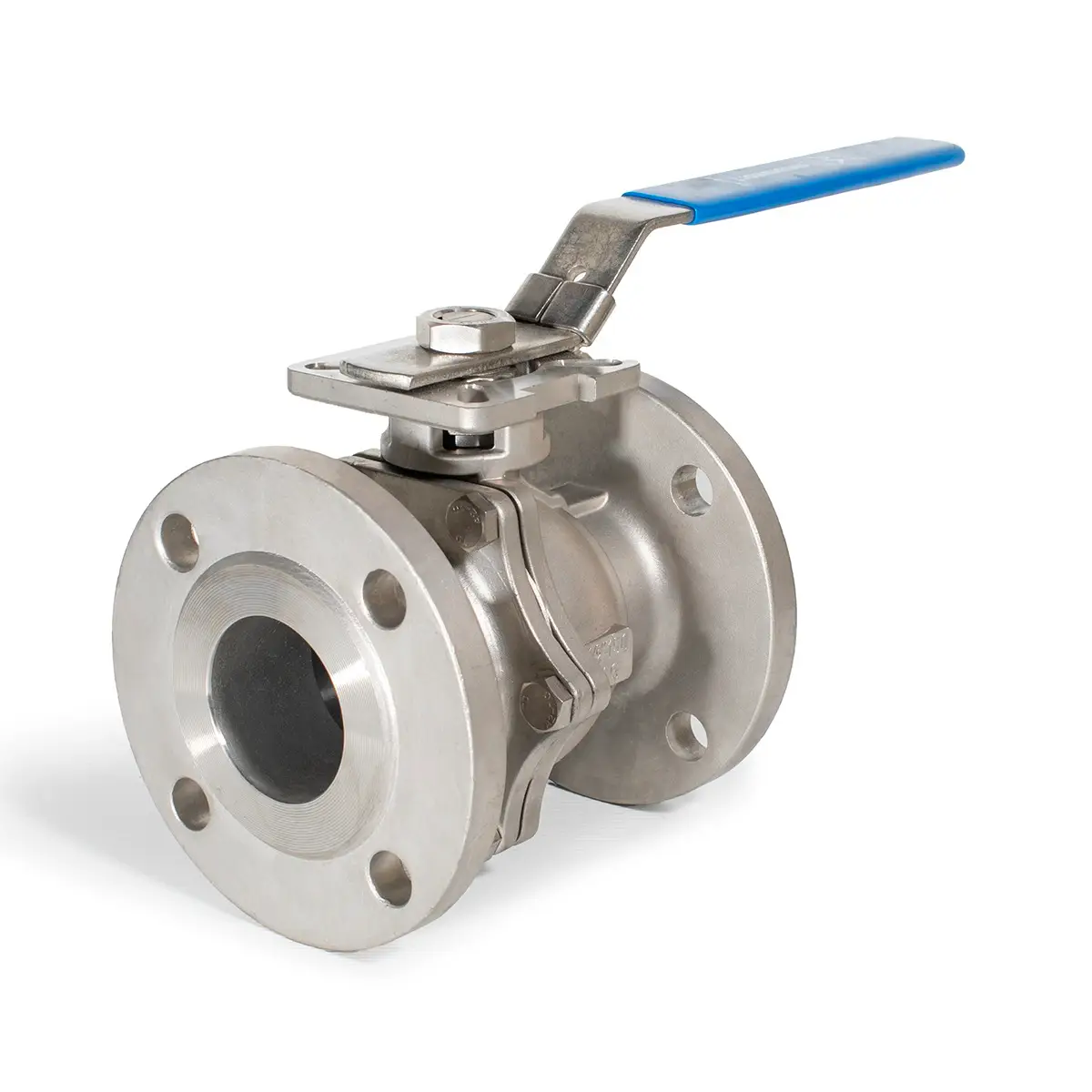
Flanged ball valves differ not in the number of pieces but in the method of connection to the pipeline. They feature flanges on either end of the valve body, which are bolted to corresponding flanges on the piping. Flanged ball valves are easier to install and remove than threaded types, making them ideal for large-scale or industrial applications where reliability and ease of maintenance are critical.
Ball Valves Advantages and Disadvantages
To assist in informing you when selecting the right valve for your application, we’ve listed the advantages and disadvantages of ball valves below:
Advantages of Ball Valves
High efficiency
Due to the size of the opening in the ball, ball valves are considered high recovery valves since they have a low-pressure drop and high flow capacity. There is little turbulence or resistance to fluid flow when the valve is fully open.
Convenient usage
As a result of their simple quarter-turn (90-degree) operation, ball valves are efficient and convenient to use. As the valve is relatively lightweight and small, it is also easy to install and remove.
Low maintenance
Compared to other types of valves, ball valves are simple and require less maintenance. Because the ball valve stem rotates without axial movement, the packing seal on the valve stem does not easily wear or fail. Ball valves are easy to disassemble and repair, and worn parts can be easily replaced.
Cost-efficient
The cost of ball valves is affordable compared to more complex valve types. Also, as they have low maintenance needs, they’re cheaper to maintain.implement in the long term.
Robust
Ball valves are among the most robust valve types because of their ability to withstand high pressures. Their wide range of materials enables them to be used in a variety of environments across a variety of industries.
Disadvantages of Ball Valves
Prone to blockages
As a result of the cavities around the ball and seats, they are not suitable for slurry applications. Slurries or other thick liquids tend to solidify or clog inside of the valve cavities, causing a significant increase in the operating torque and, in some cases, rendering the valve inoperable.
Struggle with long term throttling
Ball valves should only be used in either a fully open or fully closed position and should not be used for long-term throttling. As well as having limited accuracy in controlling flow rate, operating in a partially open position for long periods of time can cause the soft seats of the valve to deform around the edge of the hole in the ball, possibly causing it to become locked in that position. Modern design ball valves are available with a special “V” port shaped ball that can provide precise flow control characteristics.
Summary
Ball valves are simple mechanical devices used to control the flow of fluids through piping systems. Their cost-effectiveness and convenience make them ideal for most industrial applications. Their characteristics make ball valves well-suited to a wide range of applications and environments.
Despite their limitations, they are often the best choice when looking for an efficient and economical valve solution. Knowing the advantages and disadvantages of ball valves could help you select the right valve for your application. Need more advice? John Valves can help.