Ensuring your butterfly valves dimensions are the right size and correctly installed is important for optimal performance and reliability. This guide covers the essentials of butterfly valve dimensions, including sizing, types, applications, and measurement techniques.
What are Butterfly Valves?
A butterfly valve is a type of quarter-turn valve used in fluid control systems to regulate the flow of liquids or gases through a pipeline. It gets its name from its appearance, which resembles a butterfly.
The basic design of a butterfly valve consists of a flat circular disc (the “butterfly”) mounted on a shaft. When the valve is open, the disc is positioned parallel to the direction of flow, allowing for unobstructed flow passage. When the valve is closed, the disc is rotated 90 degrees to block the flow completely.
Butterfly valves are known for their simplicity and ease of operation, making them ideal for applications where quick and efficient flow control is required. They come in various sizes, materials, and configurations to suit different applications and can be operated manually or automatically using pneumatic or electric actuators.
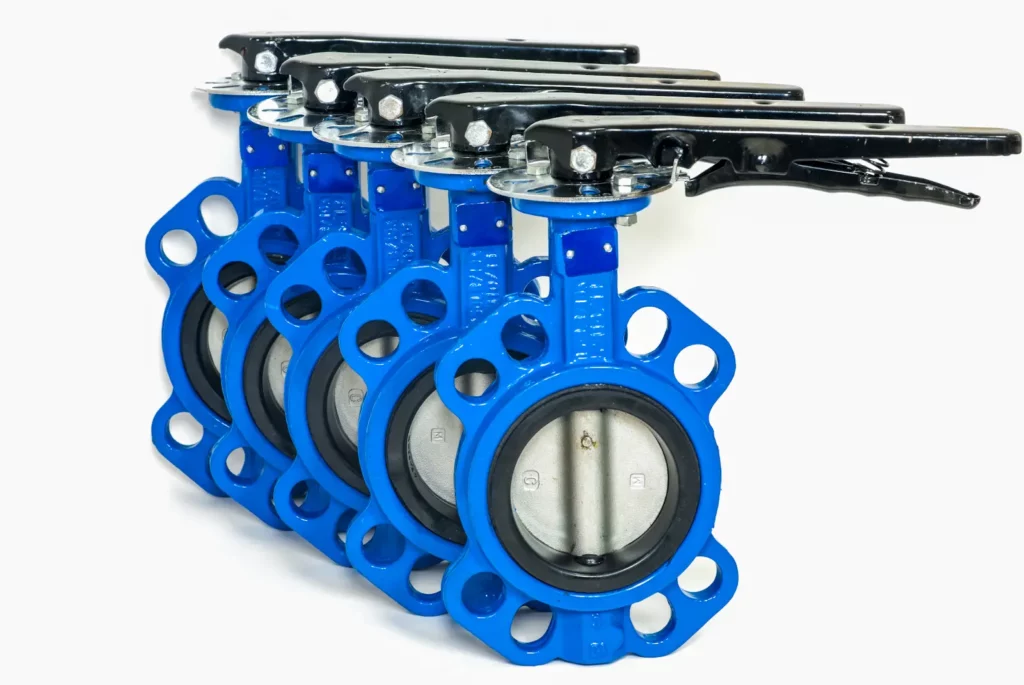
Importance of Accurate Dimensions
Accurate dimensions play a pivotal role in the performance and reliability of butterfly valves for several critical reasons:
- Perfect Fit: Precise measurements guarantee that the butterfly valve fits accurately within the pipeline.
- Flow Control: Correct valve sizing is the key to effective flow control. An undersized valve can struggle to handle fluid flow, leading to pressure irregularities and potential system inefficiencies.
As such, precise dimensions help ensure your butterfly valve operates seamlessly, fits flawlessly, and safeguards your system’s effectiveness.
Types of Butterfly Valves
Butterfly valves are mainly of three types:
- Wafer valves.
This type of butterfly valve is designed to fit between two flanges and is commonly used in pipelines where space is limited. It has a slim profile and is relatively lightweight. Wafer butterfly valves are held in place between the adjacent pipe flanges with bolts, and they do not have a lug or flange on the body for bolting. They are often less expensive than lug-style or flanged butterfly valves and are suitable for applications where the valve can be easily removed for maintenance. - Lug valves.
Lug-style butterfly valves have a body with lugs (projections) that allow them to be bolted onto the pipeline flanges. They are commonly used in applications where the pipeline needs to be dismantled frequently for maintenance or where one end of the valve needs to remain connected while the other end is worked on. They provide a more secure connection compared to wafer-style butterfly valves. - Flanged valves.
Like lug-style valves, flanged butterfly valves provide a secure connection to the pipeline as flange bolts and nuts are used for the connection. Flanged butterfly valves are frequently used in larger size installations as they are easier to fit and align when installing into the pipeline. Their body design also allows for a variety of sealing configurations to be provided.
Configurations and Applications
Butterfly valves, with their adaptability and versatility, can be configured in various ways to suit the specific demands of diverse applications. While most butterfly valves share a basic design, consisting of key components like the body, stem, disc, seat, and stem seal, what sets them apart are different types such as resilient-seated, lined, single offset, double offset (often called high-performance), and triple offset. These types vary in terms of how the disc, stem, seat, and sealing materials are designed. These differences impact how each valve performs and where it’s best suited in various applications.
Let’s explore these configurations and their practical applications in more detail:
- Concentric Butterfly Valves
These valves have a simple design with a centred disc and shaft. They are versatile and suitable for a wide range of applications, including water treatment, HVAC systems, and general industrial use. - Double Offset Butterfly Valves
Double offset valves have an offset stem and disc, reducing seal friction during operation. They are ideal for applications with high-temperature and high-pressure requirements, such as power generation and chemical processing. - Triple Offset Butterfly Valves
Triple offset valves feature a unique design with three offsets, offering excellent sealing performance and durability. They excel in demanding applications like oil and gas processing, where a tight shutoff is critical. - High-Performance Butterfly Valves
These valves are built to handle extreme conditions, including high pressures and temperatures. They are commonly used in industries such as petrochemicals, refining, and offshore drilling. - Sanitary Butterfly Valves
Designed for hygienic applications, sanitary butterfly valves are used in food and beverage, pharmaceuticals, and biotechnology industries, where cleanliness and contamination control are paramount. - Resilient-Seated Butterfly Valves
These valves feature a resilient elastomeric seat that provides a tight seal. They are commonly used in water and wastewater treatment, as well as in HVAC systems.
Understanding these differences is essential as they directly influence how each valve performs and where it’s best suited in different applications.
Critical Dimensions of Butterfly Valves
The critical dimensions of a butterfly valve are the valve diameter, disc size, stem length, and flange connection.
- Valve Diameter.
The valve diameter refers to the size of the valve’s opening or bore. It determines the flow capacity and compatibility with the pipeline. It is essential to select a valve with the correct diameter to match the size of the pipeline or the required flow control parameters. - Disc Size.
The disc size relates to the dimensions of the valve’s disc, which plays a vital role in controlling the flow of fluid. It affects the valve’s throttling capability and shut-off performance. The disc of the valve should be smaller than the bore of the adjacent piping to ensure that the valve can operate correctly without interference. - Stem Length.
Stem length is the measurement from the valve’s top to the end of the stem. It influences the valve’s reach and operability, especially in hard-to-reach or deep installations where an extension stem is required. - Flange Connection.
The flange connection dimensions ensure the valve can be securely attached to the pipeline. These dimensions must match those of the pipeline flanges for a proper fit. - Valve Length.
The length, known as the face-to-face dimension, of the valve should be the correct length to suit the spacing between the pipe flanges. A valve that is too long won’t be able to fit into the available space while a valve that is too short will have issues sealing with the pipe flanges.
These critical dimensions are pivotal in selecting the right butterfly valve for a specific application. An accurate match ensures optimal flow control, reliable sealing, and seamless integration within the system.
Measuring the Diameter
Measuring the valve diameter is a straightforward process and can be accomplished using several common tools, including:
- Ruler
A standard ruler or tape measure is a practical tool for measuring the diameter. Simply place the ruler across the widest part of the valve’s opening and read the measurement. - Calliper
A vernier calliper or digital calliper offers increased accuracy. Gently insert the calliper jaws into the valve’s opening and take the reading from the display. - Micrometre
For the highest level of precision, a micrometre can be used. Place the micrometre’s anvils on opposite sides of the valve’s bore and read the diameter from the micrometre’s scale.
Ensure that the measurement is taken at the widest point of the valve’s opening to get an accurate diameter reading. Accurate measurement of the valve diameter helps in selecting a butterfly valve that will fit seamlessly into your pipeline and provide optimal flow control.
Determining Disc Material
The application and type of fluid are two crucial determinants in selecting the disc size and material.
- Disc Size.
The disc size should be slightly smaller at the piping interface than the bore of the adjacent piping to allow for the disc to rotate to the fully open position. - Disc Material.
The disc material should resist corrosion and erosion from the fluid. Common disc materials include stainless steel, aluminium bronze, and plastic.
When choosing the disc material, it is essential to consult with a valve expert to ensure the correct selection for the application.
Measuring Stem Length and Thickness
A butterfly valve’s stem length and thickness are critical dimensions that must be measured carefully to ensure proper sizing. The stem length is the distance from the valve body’s end to the stem’s end. The stem thickness is the diameter of the stem.
To measure the stem length, follow these steps:
- Disconnect the valve from the pipeline.
- Use a ruler or calliper to measure the distance from the valve body’s end to the stem’s end.
To measure the stem thickness, follow these steps:
- Use a calliper to measure the diameter of the stem.
The required extension stem length should be specified when ordering a new butterfly valve where the required operating position is at a different floor level to the pipeline.
Understanding Flange Connection Size
The flange connection size of a butterfly valve is the size of the flanges used to connect the valve to the pipeline. It is typically specified in inches or millimetres. To identify the flange connection size of a butterfly valve, look for the following information:
- The flange connection size is typically stamped on the valve body.
- The flange connection size may also be listed in the valve’s specifications.
- Once you have identified the flange connection size, you can order a butterfly valve with the correct flange connection size.
Industry Standards for Valve Dimensions
The Australian Standard AS4795 Parts 1 and 2 specifies the requirements of butterfly valves for waterworks purposes. These standards cover dimensions, materials, and performance tests for Wafer and Lug style valves (AS4795 Part 1) Flanged valves (AS4795 Part 2).
Other Australian standards relevant to valve dimensions include AS2638.1 (Gate valves for waterworks purposes – metal seated) and AS2638.2 (Gate valves for waterworks purposes – resilient installed).
On a global scale, the International Organization for Standardization (ISO) has made valuable contributions to the standardisation of industrial valves. ISO 5752, for instance, specifically addresses face-to-face dimensions for flanged butterfly valves, harmonising practices and enhancing compatibility on an international level.
Considerations for Measurement
When measuring butterfly valves, it is essential to consider the environmental factors that may affect the valve, such as temperature, pressure, and the type of fluid that is flowing through the valve. The valve may also experience wear over time, so it is important to inspect it regularly to ensure it is still operating correctly.
Best Practices for Recording
The best practices for recording butterfly valve measurements include keeping a detailed log, including the date, time, and who performed the measurements. The log should also include any observations about the valve’s condition, such as any signs of wear or damage. This documentation can help troubleshoot problems with the valve and for planning maintenance. The benefits of recording butterfly valve measurements include:
- Identifying potential issues early on
- Scheduling maintenance before problems occur
- Extending the life of the valve
- Improving safety
Get Expert Help in Selecting the Right Butterfly Valve
Butterfly valves are essential in numerous industries, offering precise flow control, efficiency, and reliability. Understanding their different types, accurate dimensions, configurations, and applications is essential for selecting the correct valve for specific needs, ensuring optimal performance and safety.
John Valves has been working with Australian businesses to ensure their operations are efficient and safe. We have been manufacturing and supplying valves for several decades and know how to measure butterfly valves accurately.
Call today to learn more about our products and services.