There are various types of check valves available in the market, each with its own distinct features and selection criteria to consider before purchasing. As different check valves serve varying purposes and applications, the selection criteria for one valve may be insignificant for another. Nevertheless, it is essential to understand the factors to consider in each type of check valve to get the right one for your application.
Different Types of Check Valves
Ball Check Valve
Ball check valves are among the most cost-effective and simple types of check valves. Their simple working mechanism makes them highly reliable and inexpensive. They are a popular choice due to their long life span and reliability in effectively sealing off the medium.
Swing Check Valve
Swing check valves are probably the most common type of check valve used in industrial applications. Swing check valves offer near full bore flow area which minimizes pressure loss across the valve. Swing check valves often can be fitted with accessories such as an open/close indicator, lever and weight, etc.
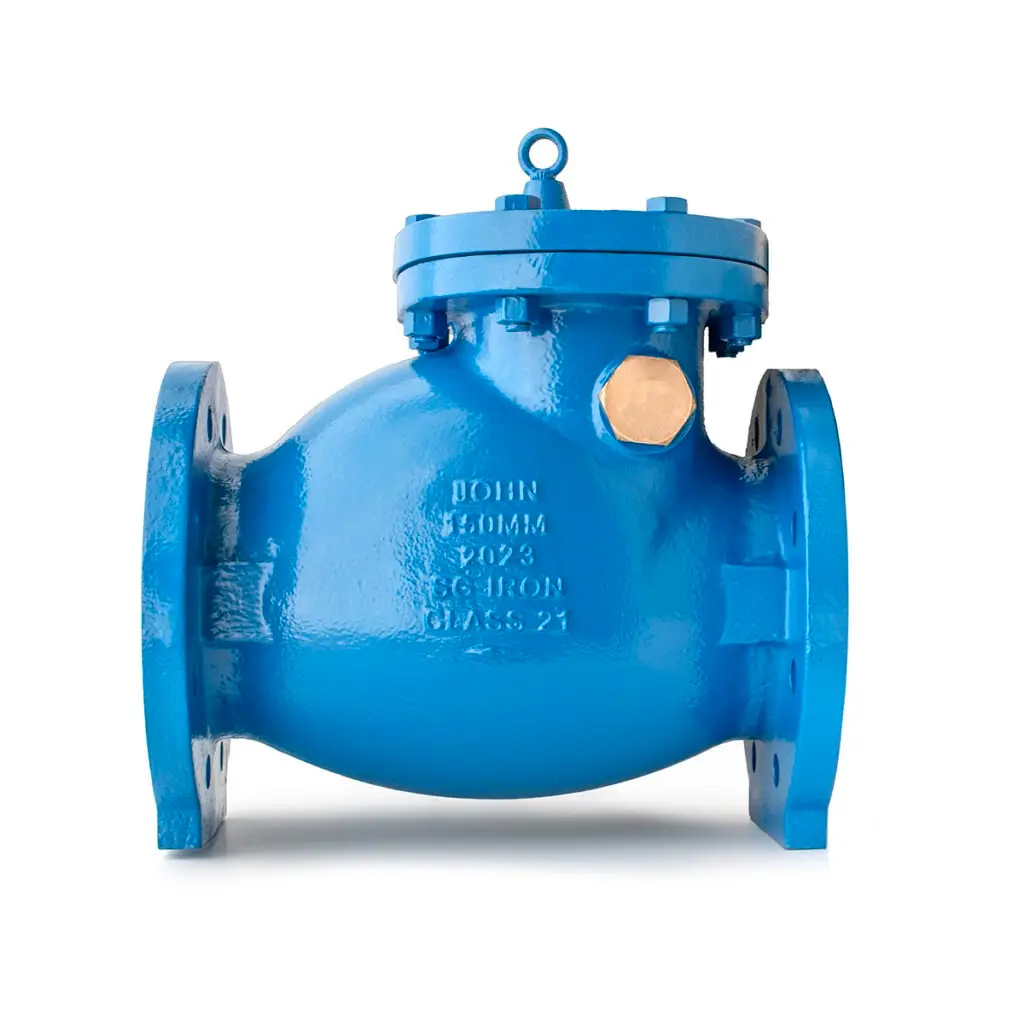
Tilting Disc Check Valve
Tilting disc check valves utilize a tilted disc and seating arrangement. They feature a short-length double-flanged valve body, making them lightweight and easy to install. The disc rotates through eccentrically positioned shafts in the horizontal and vertical axes of the body centreline. The reduced closing angle enables the tilting disc check valve to provide improved closing performance, subsequently reducing slam and pressure surges developed in the piping system on pump shutdown.
The tilting disc check valve is commonly installed in water pumping stations where multiple pumps are used and water is discharged from each pump into a common header pipe.
Tips To Guide You When Choosing The Right Check Valve
Depending on your preferred type of check valve, there are factors that you may need to consider to select the most suitable valve for your system. For best performance, it is essential to choose your valve with respect to the characteristics of each specific application.
Some of the essential characteristics to consider include:
1. Valve Size and Type
Depending on your intended application, it is critical that the type of check valve selected will meet the needed operational requirements. For instance, swing check valves are preferred where full bore flow and minimum flow resistance is required. However their closing performance is relatively poor in systems subjected to high deceleration rates when pump stoppage occurs.
Apart from the type of check valve, the size of the check valve used is also an important factor. Check valves should be sized such that they are fully open under normal flow conditions. In many situations, this means that the nominal size of the check valve installed will be less than that of the main pipeline.
2. Total Cost of Ownership
The total cost of your check valve may be significantly higher than the purchase price. For some check valves, the highest costs are the valve’s purchase price and installation costs. However, their payback comes in offering improved flow efficiency which reduces the pumping operational cost.
3. Construction Material
It is essential to consider the construction material of the check valve to ensure that the materials are suitable to withstand the chemical makeup of the flow medium. The construction material of your check valve should be compatible with the flow medium to avoid possible corrosion issues that will degrade the material of the check valve and result in a possible failure of the valve and critical damage to your system.
4. Flow Characteristics
When selecting the most suitable check valve for your system, it is essential to consider the flow rate through the valve. Each type of check valve has a recommended minimum and maximum flow velocity to ensure that the valve operates correctly and provides a long service life.
5. Performance Requirements
Different industrial processes require medium to flow at varying pressures for optimum efficiency. In applications where a liquid needs to be pumped to a high elevation over a relatively short distance of pipeline, the resultant deceleration rate of the system will be quite high once the pump stops. To prevent possible ‘slamming’ of the check valve when it closes and subsequent large pressure surges, a check valve with a high closing performance should be selected.
6. Check Valves’ Unique Requirements
Some check valves may have special requirements that your system does not meet. It’s essential to consider the cracking pressure required and the minimum flow rate required to keep the disc of the check valve in a stable operating position.
7. Maintenance
Maintenance requirements are different with the various types of check valves available. Some check valves can be maintained easily with basic tools and minimal required replacement parts. More complex design valves however require special tools to allow for the removal of seat rings, discs, etc and to gain access to the internal components of the valve.
Summary
Knowing specific information beforehand is the trick to figuring out which check valve is ideal for your application. Nevertheless, the process can be confusing for people with little or no experience working with check valves. There will always be unique complications in application requirements, chemical compatibility, and operating conditions.
Fortunately, there are experts ready and willing to help you through the entire process. At John Valves, we know all about check valve types, requirements, and installation procedures.