Introduction
Plug valves, also known as cocks, are one of the oldest types of valves still in use today. They are primarily used for quick shutoff of liquid flow and are found in various industries, including oil, gas, chemical, and water services. This article will cover the different types of plug valves, their functioning, their working principles, installation guidelines, and how to choose the correct valve for your needs.
What is a Plug Valve?
A plug valve is a type of rotary valve consisting of a tapered or cylindrical plug that rotates a quarter turn to start or stop the flow. While similar to ball valves, plug valves have a more compact design and are more commonly used in specific industrial applications.
Types of Plug Valves
There are several types of plug valves, each designed for specific applications:
- Lubricated Plug Valves – Use a lubricant to reduce friction and ensure a tight shutoff. Common in industries handling hard-to-handle liquids.
- Non-Lubricated Plug Valves – Feature non-metallic liners to minimise friction, reducing the need for maintenance.
- Eccentric Plug Valves – Designed for applications that require flow control rather than just shutoff.
- Expanding Plug Valves – Used where double-blocking and sealing are required.
Lubricated Plug Valves and How They Work
What is a Lubricated Plug Valve?
Lubricated plug valves use a specialised lubricant, typically a base oil mixed with a viscosity improver, injected under pressure to reduce friction and provide a seal between the valve’s seating surfaces. While highly effective, they require regular maintenance and are best suited for applications with infrequent operation.
Working Principles of Lubricated Plug Valves
Lubricated plug valves feature a cavity through the plug’s centre, sealed at the bottom. A sealant injection fitting at the helm allows lubricant to be introduced. The lubricant prevents sticking and provides a hydraulic force that helps lift the plug, making it easier to operate.
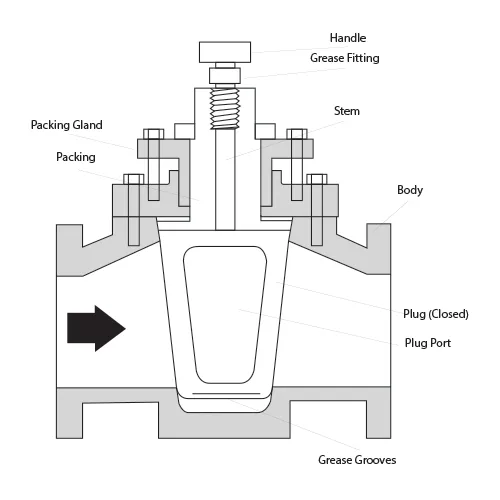
Key Aspects of Lubricated Plug Valves:
- Lubricant Injection: Ensures smooth operation and extends valve life.
- Sealant Retention Grooves: Maintain a continuous seal.
- Lubricant Compatibility: This must be selected carefully to avoid contamination or degradation.
- Regular Maintenance: Essential for optimal performance.
Installation Guidelines for Lubricated Plug Valves
Proper installation of a lubricated plug valve is essential for its functionality and longevity. Follow these steps to ensure correct installation:
- Pre-Installation Checks
- Ensure the valve specifications match the application.
- Check the identification details on the nameplate and casing.
- Do not remove protective wrappings until ready for installation.
- Inspection
- Examine the valve for any damage from transportation or storage.
- Remove end protectors and check for cleanliness and undamaged flange serrations.
- Clean the valve of any debris or scaling before installation.
- Mounting Considerations
- Plug valves can be installed horizontally or vertically but should not have the operator positioned underneath to prevent sediment accumulation.
- Support the pipeline to minimise vibrations and stress on the valve.
- Avoid excessive tightening of end flanges to prevent damage.
Differences Between Lubricated and Non-Lubricated Plug Valves
The primary difference between these two types of plug valves lies in their sealing mechanism and maintenance requirements:
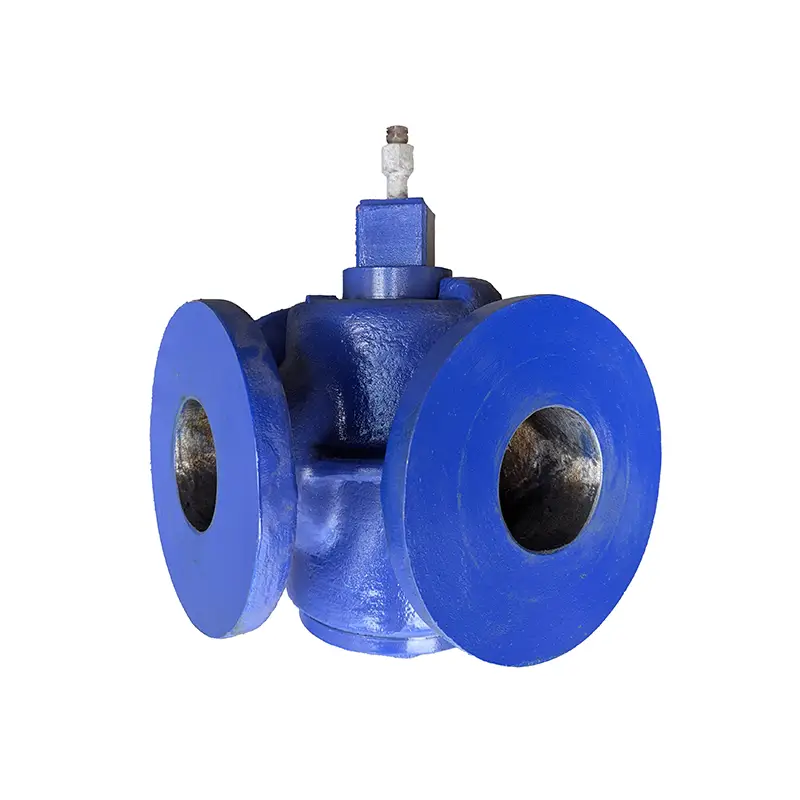
- Lubricated Plug Valves:
- A lubricating system restores the valve seat and extends its longevity.
- Require regular maintenance to ensure proper lubrication.
- Suitable for high-temperature and high-pressure applications.
- Non-Lubricated Plug Valves:
- Feature thermoplastic or elastomeric liners to reduce friction.
- Require minimal maintenance.
- They are not suitable for high-temperature applications due to their non-metallic seats.
Choosing the Best Plug Valve for Your Needs
Selecting the correct plug valve is crucial for ensuring efficiency and longevity in your system. Consider the following factors:
- Flow Medium Compatibility: Ensure the valve materials and lubricants are suitable for handling the liquid or gas.
- Operating Conditions: High-temperature and high-pressure environments require specific valve types.
- Maintenance Requirements: A non-lubricated valve might be a better choice if regular maintenance is not feasible.
- Installation Environment: Ensure the valve can be mounted appropriately based on your pipeline layout.
Lubricant Sticks for Plug Valves
Sticks of lubricant are a common method for maintaining lubricated plug valves. These solid lubricant sticks are inserted into the valve through designated injection points, where they gradually dissolve under pressure to provide continuous lubrication. John Valves can supply lubricate to suit your needs.
Benefits of Lubricant Sticks:
- Consistent Lubrication: Ensures even distribution throughout the valve.
- Reduced Maintenance Effort: Requires less frequent reapplication compared to liquid lubricants.
- Prevents Wear and Tear: Protects valve components from friction and corrosion.
- Enhanced Sealing: Helps maintain a tight shutoff and prevents leaks.
Application Process:
- Identify the lubrication injection port on the valve.
- Insert the lubricant stick into the port.
- Apply pressure as recommended by the manufacturer to ensure proper dispersion.
- Monitor lubrication levels periodically and replace sticks as needed.
Using lubricant sticks can improve the longevity and efficiency of lubricated plug valves, particularly in applications where consistent performance is critical.
Conclusion
Plug valves are essential in many industrial processes, offering efficient shutoff capabilities. Understanding the different types of plug valves, their working principles, and proper installation guidelines can help you select the correct valve for your needs. If you require assistance choosing the best plug valve for your system, visit our website or contact us today to book an appointment.