Parallel slide valves are used mainly on high pressure and temperature applications. These valves are heavily deployed in the steam generation, petroleum and natural gas industries. The valves are available in different configurations such as bolted bonnet, pressure seal, and welded bonnet parallel slide valves, each catering to specific use cases.
In this blog, you’ll find maintenance guidelines, troubleshooting steps, and safety precautions for the proper upkeep of parallel slide valves needed to achieve maximum efficiency.
Get ready to empower your industrial processes.
Importance of Parallel Slide Valves in Industrial Applications
Parallel slide valves are essential in industrial applications due to their exceptional sealing capabilities and operational performance. Making them invaluable in industries such as steam turbine power plants and high-pressure steam systems. Their ability to provide reliable sealing ensures:
- Optimal performance
- Reduced energy consumption
- Prolonged equipment lifespan.
Unlike other conventional wedge gate valves, parallel slide valves utilise two gates or discs that slide parallel to each other to control the flow. The superior sealing also prevents contamination and safeguards the system’s integrity.
Types of Parallel Slide Valves
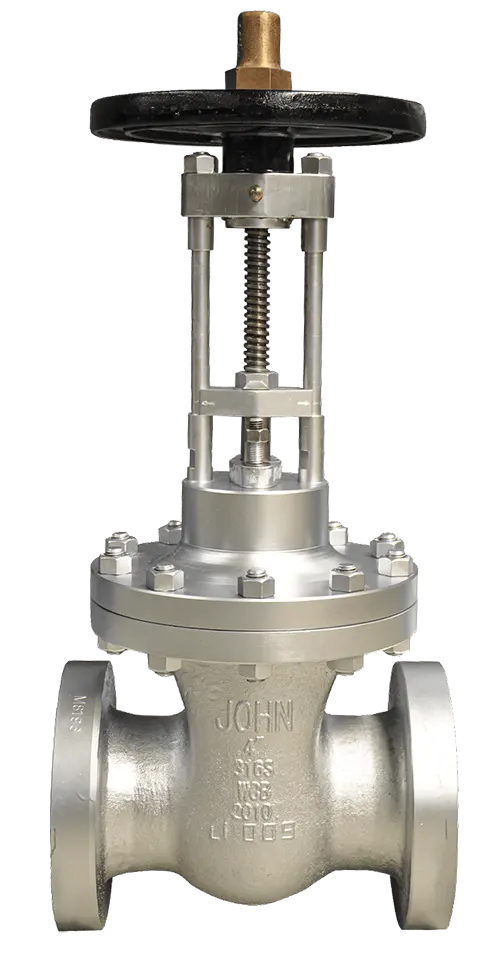
Parallel slide valves come in various configurations to meet the specific demands of different industrial applications:
Bolted Bonnet Parallel Slide Valves
Bolted bonnet parallel slide valves are commonly used in steam generation industries that are operating at low to medium pressures. They feature a bonnet bolted to the valve body, facilitating easy disassembly and access to internal components for maintenance purposes.
This design allows the convenient replacement of worn-out parts and routine inspections, ensuring the valve’s longevity and reliability.
Pressure Seal Parallel Slide Valves
Pressure seal parallel slide valves are specifically designed for high-pressure applications. They incorporate a pressure seal bonnet that provides a secure and leak-proof seal, even under extreme pressure conditions.
These valves find widespread use in industries like power generation, oil and gas refining, where systems operate at high pressure and maintaining system integrity is critical.
Welded Bonnet Parallel Slide Valves
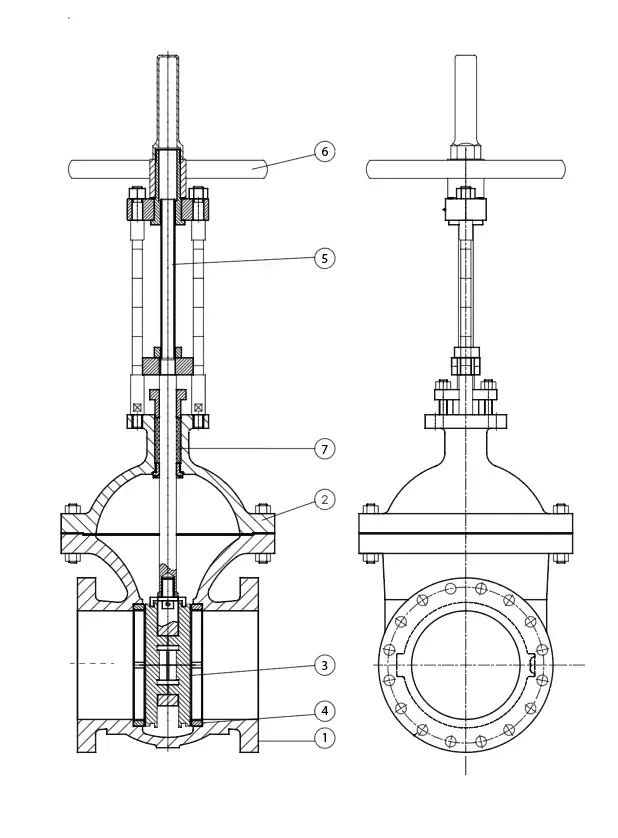
Welded bonnet parallel slide valves are known for their exceptional strength and durability. The bonnet is directly welded to the valve body, creating a robust and leak-resistant seal.
These valves are often preferred for heavy-duty applications that require reliable performance and resistance to harsh operating conditions. They are usually provided in smaller sizes.
Applications of Parallel Slide Valves
Parallel slide valves play a pivotal role across industries, offering precise fluid control in demanding environments. Here are some of the most common applications of parallel slide valves:
Utilisation in High-Pressure Steam Systems
Parallel slide valves are vital components in high-pressure steam systems, where precision flow control is paramount. In these systems, they excel at isolating the flow of steam. This capability is crucial for power generation and various industrial processes that rely on steam, such as chemical manufacturing or food processing. The ability to control steam flow accurately ensures that the systems operate efficiently and safely, preventing overpressure situations.
Implementation in Oil and Gas Pipelines
In the oil and gas industry, parallel slide valves are primarily used for dependable shutoff, ensuring that the flow of oil or gas is properly controlled. Their robust design and exceptional sealing capabilities are critical for preventing leaks, which could lead to environmental hazards and significant financial losses. Parallel slide valves play an important role in maintaining the security and integrity of fluid transport in pipelines, safeguarding both the environment and industry assets.
Role in Power Generation Plants
Power generation plants heavily rely on parallel slide valves to manage steam flow within turbines. The precision and resilience of these valves are essential for optimising the efficiency of power generation processes. By controlling the flow of steam to the turbines, parallel slide valves help regulate the generation of electricity, ensuring that power plants operate at peak performance. This not only enhances the plant’s overall efficiency but also contributes to a stable and reliable electricity supply for various industries and households.
Working Principle of Parallel Slide Valves
Parallel slide valves are operated by moving the two gates or discs linearly within the valve body. When fully closed, the gates utilise the system pressure to create a tight seal, minimising leakage and ensuring optimal performance.
How Parallel Slide Valves Operate
Parallel slide valves operate by sliding the gates across the seat faces within the body of the valve to either isolate or allow the flow of liquids or gases. When the gates are in the closed position, they seal off the flow completely. Opening the valve involves sliding the gates across the body seats to create an unobstructed pathway for the fluid to flow through.
Advantages of Parallel Slide Mechanism
The parallel slide mechanism offers several advantages in industrial applications, such as:
- Excellent sealing capabilities, minimising leakage and ensuring system integrity.
- The prevention of thermal locking due to fluctuations in fluid temperature.
- Low operating torques allowing for smaller actuators to be used thereby reducing cost and energy usage.
- Simplified maintenance and reduced risk of jamming or sticking.
- Reliable and long-lasting performance.
Essential Maintenance Guidelines
Proper maintenance is vital for the long-term performance of parallel slide valves. Regular inspection, lubrication, and addressing wear issues are essential to ensure the system’s integrity.
Regular Inspection and Lubrication
Frequent inspections of valve components, such as the gates and body seats, are necessary to identify potential issues. Lubrication of the operating stem with appropriate high-temperature grease maintains smooth operation and minimises friction-induced wear and tear.
Addressing Wear and Leakage Issues
Wear and leakage are common challenges. Replacing worn packings and seals while addressing minor leaks promptly prevents more significant problems. Periodic pressure testing and re-machining can restore valve sealing efficiency.
Valve Overhaul and Component Replacement
Scheduled overhaul involving disassembly, cleaning, and reconditioning is essential. Critical components like the gates or discs should be inspected and replaced readily depending on the severity of applications.
Common Problems and Troubleshooting
Some common problems related to parallel slide valves include:
- Discs becoming jammed due to debris accumulation
- Uneven wear or scoring on the sealing surfaces
- Leakage from damaged packings or seals
Identifying Common Valve Malfunctions
Detecting problems requires examining parallel slide valve movement irregularities, fluid leaks, and abnormal temperature changes. Identifying these signs aids in pinpointing specific malfunctions.
Safety Precautions During Maintenance
Maintenance of parallel slide valves requires strict adherence to safety protocols. This will not only ensure the safety of workers but also prevent any damage to the equipment. The following factors are crucial in maintaining a safer environment during maintenance activities:
- Proper training for overhauling valves and other system components.
- Use of personal protective equipment (PPE) and suitable tools.
- Skills in troubleshooting high-pressure systems.
Ensuring Safe Valve Handling
When handling valves, it is essential to use proper tools and equipment for lifting heavy components, maintain a clear work area, and avoid tripping hazards. Verify system isolation to prevent unintended flow during maintenance.
Proper Lockout/Tagout Procedures
If the valve is still installed within the line, implement lockout/tagout procedures to isolate energy sources and prevent accidental valve activation. Each worker involved should place their lock/tag to ensure collective safety. Confirm energy isolation before commencing any maintenance activities.
Best Practices for Prolonging Valve Life
Optimal valve life can be achieved through the following practices:
- Ensuring correct installation and alignment.
- Regular preventive maintenance and responsive repairs are critical factors in extending valve longevity.
Correct Installation and Alignment
Accurate valve installation includes proper gasket placement, torque application, and alignment with connected piping. Precise alignment minimises stress, leakage, and operational inefficiencies, contributing to prolonged service life.
Implementing Preventive Maintenance Plans
Schedule inspections, cleaning, lubrication, and component replacements as per manufacturer guidelines to prevent degradation. Early detection of wear, corrosion, or potential issues through regular maintenance extends the overall durability and reliability of the valve system.
Also read: Parallel Slide Gate Valves Vs. Wedge Gate Valve
Work With John Valves for the Extended Life of Your Systems
Unlock the full potential of your industrial processes and ensure the lasting integrity of your systems with John Valves’ dependable parallel slide valve solutions. Our commitment to quality and decades of expertise have made us a trusted partner for Australian businesses, consistently meeting diverse demands and exceeding industry standards.
Don’t compromise on efficiency or system reliability. Contact us today to discover how our expert solutions can enhance your operational requirements, providing you with the peace of mind that comes from knowing your systems are in capable hands.